Author: Martin Dubé, Teacher and Researcher at Innofibre
Packages made of corrugated cardboard occupy a very large part of our everyday lives, accounting for almost 40% of the industry’s cellulosic fibre packaging. Although this type of packaging is mainly used for moving or transporting heavy items, it’s now possible to create light and highly functional packaging structures that allow to greatly increase its scope of applications.
Flutes and Microflutes
Corrugated cardboard minimally contains three distinct cardboard layers, one of which is the flute section sandwiched between two cardboard liners. The fluting is manufactured by inserting a cardboard layer in a corrugator, basically two intricated toothed rollers. The rollers are heated, allowing the cardboard to adopt a permanent corrugated shape (the flute). Afterwards, the other layers of cardboard (the top and bottom ‘cover’ liners), are assembled to the flute using a starch-based glue. More complex structures can be manufactured by adding flute sections separated by liner cardboards. The flute is classified according to its amplitude (height of the waves) and wavelength into different letter categories that are presented in Table 1. The A, B, and C – category flutes are widely used for manufacturing boxes containing products that have considerable weights, whereas the E, F, and N- category flutes fall into the microflute category which is used for packaging items as well as for showcasing products, because high quality print can be applied on its surfaces. These types of microflutes are found in the packaging of cosmetics or even fast food.
Table 1: Flute Classification of Corrugated Cardboard
Type |
Amplitude (mm) |
Number of flutes per meter(m-1, +/- 10) |
A |
4.8 |
118 |
B |
3.2 |
154 |
C |
4.0 |
128 |
E |
1.6 |
295 |
F |
0.8 |
410 |
N |
0.5 |
560 |
Waves That Give Structure
Corrugated cardboard plays multiple roles. One of which is to protect packaged goods from shocks and vibrations owing to the potential crushing resistance of the flute. This property is measured using the traditional Concora Corrugating Medium Test (CMT) which estimates the potential flat crush resistance of a corrugated board. But most importantly, corrugated cardboard conveniently integrated into the structure of a box, will give it more rigidity and resistance, allowing it to be stacked under other boxes.
Rigidity mainly depends on the elastic modulus of the external elements, and especially, to their distance in relation to the flexion centre; that is to say, the thickness of the structure. One of the main roles of corrugated cardboard is thus to provide a support and a regular spacing between the liners to increase the box’s rigidity. The axe of the flute, being perpendicular to the machine direction (MD) of the cardboard (Fig. 1), allows for the top and bottom covers to benefit from this added rigidity. On the other hand, the resistance needed to stack boxes comes from the fact that the sides of the box are oriented in the board cross direction (CD). The edgewise compression strengths (Edge Crush Test (ECT)) of the cardboard and of the flute add up together, increasing the resistance strength of the boxes during stacking.
Microflutes Provide Corrugated Cardboard with New Functionalities
The microflutes (types E, F, and N) make up almost 10% of the corrugated cardboard market, with growing popularity expected in the years to come. Corrugated cardboard that are made of microflutes are light, resistant, and offer an excellent print quality thanks to the small spacing between the waves within the flute. These are mostly found in the packaging of relatively lightweight products, such as shoes, dishes, small household appliances, etc. for which the visual appeal of the packaging is very important. Also, the rigid structures at the base of the microflutes can form stands that are used for display in groceries, pharmacies, or hardware stores. We can even find microflutes in food packaging, including closable hamburger containers (clam-shell) from certain fast-food chains.
The current trend in microflutes, as well as for the entire corrugated cardboard industry, is related to the reduction in grammage. It is often below 100 g/m2 (20 lb/1000 pi2) for microflutes, whereas for corrugated cardboards, it is typically in the order of 112 g/m2 (23 lb/1000 pi2). In addition to influencing the performance of the corrugator machine, such low grammage impose that new means be used for testing the cardboard. For example, the Short Span Compression Test (SCT, alias STFI) becomes very important, whereas the Concora Test that determines the potential flat crush resistance of corrugated papers (Concora Corrugating Medium Test, CMT) becomes extremely difficult to perform with grammage that are less than 100 g/m2.
Over the last year, online markets have experienced massive growth, and this trend seems to be leaning towards exponential growth. It is now more pertinent than ever to develop lighter and more solid packaging structures. Innofibre, with its team of researchers, is actively participating in the development of these new grades of cardboard to meet industrial needs.
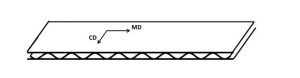
Figure 1: Representation of the Base Unit of a Corrugated Cardboard. The Flute is Located Between Two Cover Layer Cardboards.
Figure 2: Sizes of the Flutes (A, B, C) and Microflutes (D, E, F, N).
Source : cvpack.com