Author: Wendy Rodriguez Castellanos
Cellulose packaging is booming. In recent years, we’ve seen the arrival – on the Quebec market – of cellulose packaging from other regions of the world. Most of this packaging is made from non-wood fibers such as bamboo or bagasse.
By 2021, the packaging sector accounted for 52% of the global market of the Pulp and Paper industry, valued at $351.5 billion. According to experts, this market is growing at an annual rate of 4% due to demographic growth and changes in retail consumption patterns.
By 2022, the global annual growth of cellulose packaging derived from non-wood fibers had reached an impressive 7.2%, outpacing the growth rate of 5.4% observed for packaging sourced from wood fibers. Additionally, the recent spate of forest fires has affected the availability and exploitation of forest resources.
To address this challenge, the experts at Innofibre have intensified their research efforts on pulping processes and investigating alternative biomass sources. These endeavors aim to identify competitive sources of cellulose pulp suitable for thermoformed cellulose packaging. The Innofibre team is now working on scaling up recipes and processes employing alternative biomasses available in Quebec and Canada to accelerate the technology transfer to industry.
What are non-wood fibers?
Non-wood fibers are classified as bast fibers, grass fibers, leaf fibers and fruit fibers. Bast fibers are well known to be strong and long fibers, such as ramie, hemp, and flax. Grass fibers, on the other hand, are obtained from the stems and leaves of monocotyledons (plants whose seedlings, after germination of the seed, initially have only one leaf, called a cotyledon), such as bamboo, bagasse, wheat straw and switchgrass, among others. As for the leaf fibers, the most common ones include sisal and abaca, which are plants that grow in the warm regions of the world. Finally, fruit fibers are obtained from seed or fruit hairs.
With such a variety of sources and characteristics, processing non-wood fibers to obtain cellulose pulp presents some issues concerning the collecting of raw materials, their pre-treatment, and the processing conditions during pulping.
Non-wood fibers available in Quebec and Canada
History has taught us that replacing one raw material with another without caution, will result in shortages in the medium term, especially now, as the market for cellulose packaging is rapidly expanding. Therefore, using local biomasses to produce cellulose pulp would simultaneously minimize environmental damages and the impacts on food chains, in addition to meeting market demands.
Consequently, to meet the need for replacing certain single-use plastics, without neither damaging the environment nor affecting the food chain that depends on annual plants, the use of rapid-growth renewable biomasses or of residual biomasses to produce packaging should always be privileged.
In Quebec, non-wood fibers sources include agricultural fibers, potato crop residues, cellulose residues from the food industry, and wastes from crops like hemp and flax shives. Elsewhere in Canada, agricultural residues from wheat, soybean and canola crops, have a great potential for packaging purposes.
The method for developing cellulose pulp recipes from non-wood fibers.
The extrusion process is well known in the plastics industry, where it is used to create a wide range of products, including pipes, tubes, cables, and structural shapes. It is also used for food products such as pasta and breakfast cereals. Extrusion enables mixing by high pressure and shear forces. With the adequate temperature and controlled humidity, it is possible to obtain cellulose pulps.
In a recent applied research project, experts at Innofibre studied the effects of certain engineering variables involved in the twin-screw extrusion process and the quality of the cellulose pulp made from alternative biomasses. The screw configuration, its speed, the feed rate, the biomass moisture content, the chemical treatment, the impregnation time temperature, and biomass pretreatment are some of the parameters that were controlled to identify the conditions for obtaining cellulose pulps with promising characteristics for a quality thermoformed product at a reasonable cost.
The production of thermoformed cellulose packaging using the TF-45 thermoforming equipment (with a capacity of 45 kg/h) has allowed to study the characteristics of these pulps for a large-scale production. The cycle time (the time needed to produce one item) is of major importance for the manufacturing of thermoformed cellulose packaging.
Given the diversity of non-wood fibers, characterized by variations in length and strength, the pulping process can be tailored to accommodate a wide array of biomasses. This adaptability enables these materials to emerge as viable alternative sources for cellulose fibers.
A further challenge associated with the use of agricultural fibers is their high silica content, which hinders the recovery of cooking liquor. That’s why, Innofibre is working on the development of different chemical processes along with the recovery/reuse of those chemicals. Potassium hydroxide is also used instead of sodium hydroxide, which generate a residue that can be used for the crops.
Extrusion pulping offers advantages for non-wood fibers processing, including low effluent levels, refining can be performed on the same equipment, and fines control, particularly for short fibers. In addition, fiber yields can reach up to 75%-80%.
Innofibre experts have taken on the challenges involved in pulping various types of non-wood fibers. Achieving significant yields and competitive pulp properties, while using a low environmental impact process is one of their ways of positively contributing, economically and ecologically, to the community.
More than ever, Innofibre is at the forefront of the development of cellulose packaging, providing a real option for replacing single-use plastics. Indeed, the work done by Innofibre into the process of converting non-wood biomasses into non-wood pulp by twin-screw extrusion, additionally to a decade of expertise in thermoforming cellulosic fibers, offer several opportunities of technological transfer and training program for the next generation.

Raw material
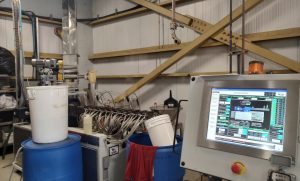
Extrusion pulping
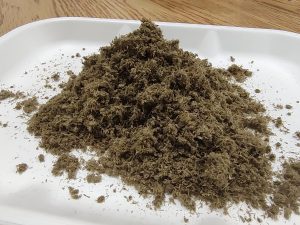
Cellulosic pulp obtained by extrusion
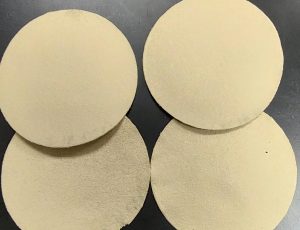
Extrusion pulping process