Author: William Belhadef, researcher at Innofibre
Is it possible to imagine a future for biocoal in the iron and steel industry? Over the past 15 years, the popularity of biocoal (commonly called charcoal) has been increasing at a rapid pace, with ten times more scientific articles being published about its production than ever before. We are witnessing a progressive return of biocoal in several fields of activities, particularly that of biochar, which is what we call biocoal intended for agricultural use. Note that biocoal is the generic term given for any form of carbonized biomass. Nowadays, climate changes caused by greenhouse gas emissions (GHG) are driving key players to use biocoal as a sensible replacement for fossil fuels in their industrial applications, including the iron and steel industries: metallurgy of iron, silicon, cast iron, steel, and ferroalloys.
Industrial Applications of Biocoal in the Iron and Steel Industry
In this industry, biocoal, plays several roles. It can, of course, be used as a reducing agent, where it provides a renewable source of carbon to reduce iron oxide ore into metallic iron. It is also used as a texturing agent, which allows for the obtention of an adequate consistency when it is added to the ore, giving the ore a good permeability to gas. Thus, biocoal is used instead of mineral coal in many steps involved in the metallurgical process.
Figure 1- Charred wood chip sample
Interest Potential for the Quebec Steel industry
At this moment, biocoal has every chance of securing its place in the Canadian steel industry. Its future is promising on account of the abundance of forest resources in addition to the presence in Canada of large iron and alloy factories, namely those in Québec, that are seeking to undergo environmental and energy transitions. The national economic impacts of using biocoal are threefold: it will reduce dependency on fossil fuels, and it will support the local forestry industry by providing an additional outlet for their residual biomass. Finally, it will contribute to improving global issues, that is, by reducing GHG emissions.
The steel industry has the opportunity to move toward a greener future by directly or indirectly integrating biocoal production and setting aside coal from fossil origin. It’s a fact: the demand for green steel is greater than ever and global efforts are taking place to find innovative ways for using biocoal at an industrial level. A perfect example of these innovations is the construction of the HYBRIT demonstration furnace in Luleå, Sweden, which uses fossil free hydrogen. It’s now a known fact that within the biocoal production process, it’s possible to generate hydrogen as a co-product. Indeed, while biomass is being transformed into biocoal, free volatile compounds and bio-oils are also generated, and later used for producing hydrogen.
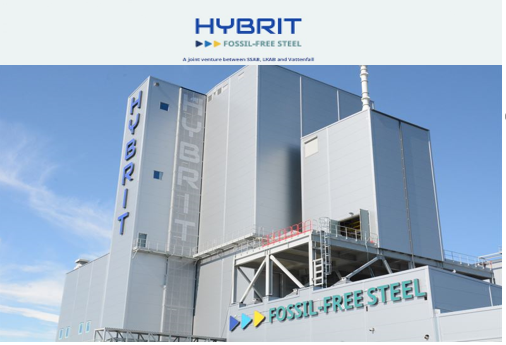
Figure 2: The HYBRIT project in Sweden (Credit SSAB)
Not just any Biocoal Obtained any Which Way
Because tonnage requirements in the steel industry are substantial, it’s essential to aim for high yields when converting biomass into biocoal. Biocoal is obtained by heating biomass at temperatures ranging between 300 and 600 °C, in an oxygen-deficient atmosphere. The heating time will vary from a few seconds to several days, depending on the technique being used and the biomass particle size.
But that’s not all as far as chemical properties are concerned. The biocoal for the iron and steel sector must be almost identical to coke or anthracite (hard coal), i.e., it must have a high content of elemental carbon without any volatile compounds. Volatile compounds are gases adsorbed or trapped within coal pores that are essentially carbon dioxide, carbon monoxide, methane, and light hydrocarbons. Steel producers try to limit these compounds to a minimum because their release disrupts the steelmaking process. Moreover, these gases are responsible for a self-heating phenomenon that can lead to spontaneous self-ignition during storage or transportation of biocoal.
In practice, the transformation process of biomass into biocoal implies an antagonistic relationship between reaching high transformation yields and obtaining the sought-after chemical properties. Although science and technology have largely contributed to the ongoing development of biocoal characterization, which allows for a better understanding of its transformation, at least in part, the plethora of physicochemical reactions involved are still not fully understood.
The major challenge is to discover and optimize some new strategies for transforming biomass into biocoal for the purpose of simultaneously obtaining large amounts of elemental carbon, low quantities of trapped volatile compounds, and a high yield. The Innofibre team is currently testing different paths with industrial partners to find solutions that will meet their criteria in terms of product characteristics and process.
Figure 3 – Volatile compound measurements according to ISO 18123, an empirical method for determining biocoal mass loss at 900 °C for 7 minutes.
A Task Force Dedicated to Biocoal
Innofibre has put in place an elite operational group in applied research that focuses on characterizing and producing specific biocoal. This team is made up of researchers and technicians that are dedicated to the pre-treatment of biomass and its various thermochemical conversion processes. The work is being carried out in a pilot plant where a wide range of pilot and laboratory equipment is used to develop biocoal, with masses that range from a few grams to several tons. The laboratories are equipped with analytical instruments that allow to characterize both the biomass collected as well as the gases that are emitted during the conversion process.